TECHNOLOGY
Air Micronization of Soft Materials
Ultra Fine Milling Technology Today
The demand for finer and dry products has increased world- wide. Fine particles are so important for covering large surfaces with a thin layer of solids (e.g. coatings), and also for increasing dissolution rates (e.g. pharmaceuticals). This has led to the development of certain dry grinding processes to achieve submicron fineness. The new innovations that have being made are in the area of “fluidized bed air jet milling”. Best results with this process uses super heated steam with speeds of up to 1,200 m/sec as milling gas, and final fineness in the submicron range (example: D50 > 5.0 micron) can be reached.
Compared to compressed air with speeds of about 550m/sec., steam provides considerably higher jet energy. The kinetic impact energy of the particles inside the fluid bed rises fourfold. Steam moves at a higher speed of sound than air. The circumferential speed of the current inside the classifier does rise, which in turn influences the acceleration forces effecting the material during classification after milling. Today, the frequently used air jet milling system used for the extreme particle reduction of powders to the order of 0.2 – 5 micron are propelled with compressed air
Pulverization takes place in the central chamber of the air jet mill. The particles are passed into the grinding chamber via a special feeder which controls the feed rate. Particles are accelerated and driven at near sonic velocity around the perimeter of the toroidal chamber by multiple jets of air or steam. No grinding media is involved. The process material undergoes extreme turbulence to high pressures and velocities generated from the air flow introduced via special nozzles.
The turbulence and orbital nature of the grinding chamber ensures multiple particle – particle interactions at a high frequency. As the particles are reduced in size, they progressively lose mass and eventually migrate towards the centre of the milling chamber from where they are discharged. The larger particles remain at the exterior area of the chamber.
The feed rate of the material into the air jet mill determines the morphology and the broad distribution of size ranges of the particles. Notably, the particles do undergo significant particle size reduction at a lower feed rate, with reduced yields.
Typical parameters:
- Diameter of mill: from 0.05 m to 1 meter
- Gas pressure: 8.3 Bar (120 PSI)
- Starting particle size: 800 microns or less
- Final particle: 0.5 to 5 microns
Fochem International’s Innovative Jet Mill Technology
The jet mills offered today have disadvantages, this explains why they are not generally used for large scale production:
Working with steam at temperatures around 300 – 400 ° C is dangerous, and also causes water precipitation in the filters and piping system and in the products. Compressed air in large volumes is expensive. A compressor has a set speed, and its output and pressure of air cannot be changed, e.g. to deliver air at higher pressures. The particle finenesses achieved with the jet mills offered today are satisfactory, but the production yields are much too low. This was the reason why FOCHEM INTERNATIONAL got engaged with the development of its own Jet Mill Technology, as large amounts of micronized graphite was needed.
After many years of trial-and error, a basically technically simple but highly efficient micronizing technology as developed that yielded considerably better results than all equipment on the market today:
- Particle sizes between 0.1 to 5 micron in large quantities can be produced,
- No use of expensive compressors, or steam generators,
- Hardly any wear of the mill (the particles to be milled wear solely against each other). The mills are operating for many years without maintenance.
- The velocity of the compressed air generated during the process is set at 1100 m/s; it can be increased above 1500 m/s.
This technology is confidential and the machines are not for sale.
Fochem Internationals`s New Bead Wet Mill Technology for the Processing of Micro Fine Graphite Dispersion
For the production of dispersions used in the coatings industry, small particle sizes of a specific shape are essential. The so-called “Bead Mills” are commonly used for the manufacture of such dispersions.Bead Mills are machines for the ultra fine grinding of solid particles in a liquid, mostly water, in the presence of small ceramic, glass- or metal beads.
There are many kinds of bead mills on the market, but none of them was found to be suitable for the production of nano fine graphite dispersions. The capacities of the commercially available mills are too small for an industrial scale production. They all work on the principle of impact (collision), destroying the crystalline structure of the graphite. The high rotation speed of the impeller causes heavy friction and wear between the milling media and the contamination of the dispersion with impurities is of major concern.
Over the years FOCHEM INTERNATIONAL have developed a new type of wet mill technology, which does not work on impart but on high pressure share. The graphite crystals are carefully de-foliated, they become thinner as the milling progresses. At the same time the specific surface area that can be covered with an x amount of graphite is enlarged. During the milling the colour of the graphite is changing from grey to bright silver. This is an indication of the presence of “Graphenes”. Ultimately our process is yielding a graphite dispersion with a close to perfect stability, superior lubricity and better die coverage. All these characteristics are essential for the improvement of the die life of our forging customers and other industries.
Our mills are very much larger than the commercially available Bead Mills, and thousands of tons of sub-micron graphite dispersions have been produced over the years.
Fochem International`s Technology used by Tribo-Chemie Germany, our sister company.
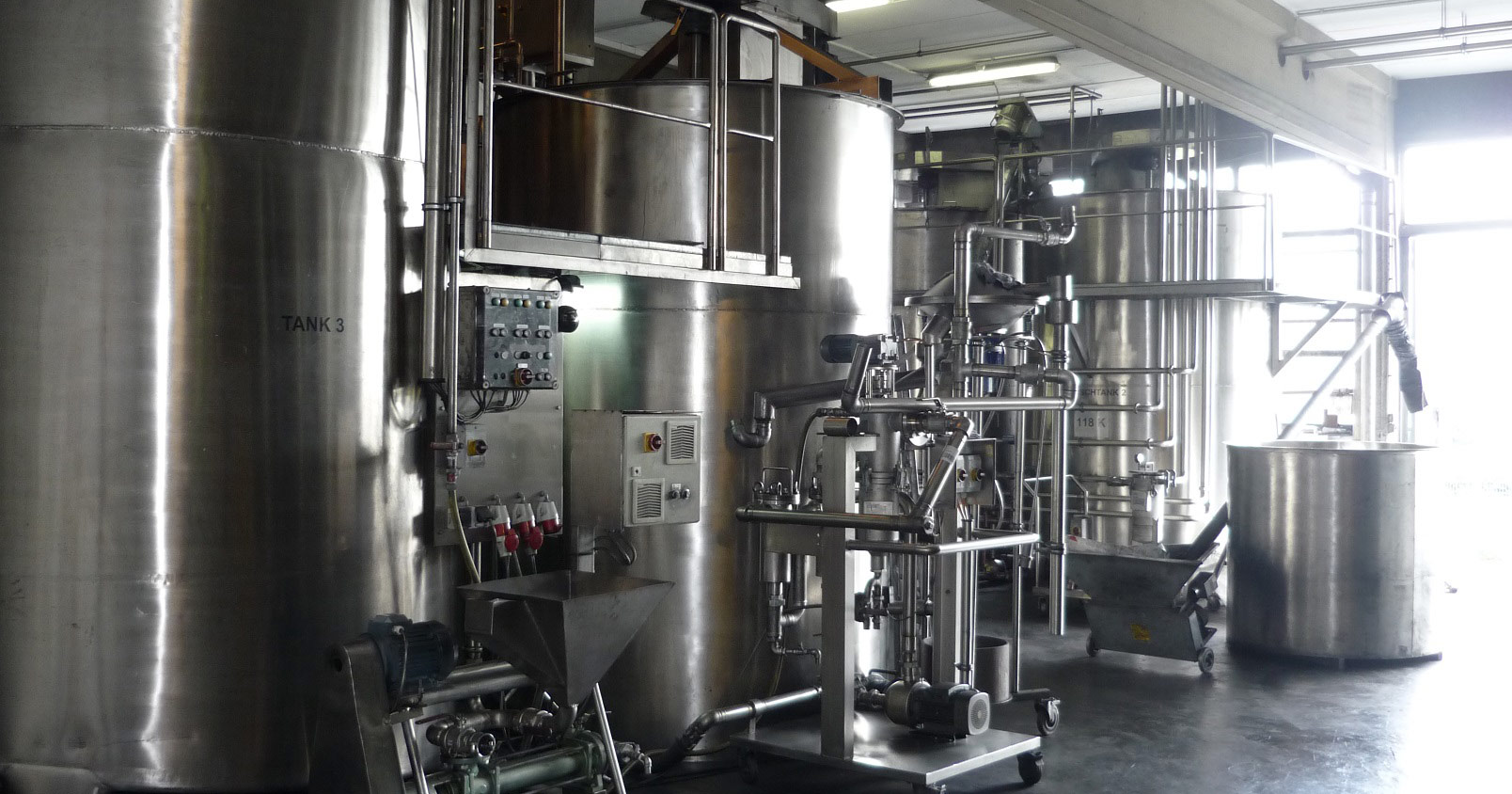
New Technology for the Production of “Hydrophobic Release Emulsions”
For the past 40 years or so, so-called water-based release agents are in use for high pressure die-casting. Most of the products are based on colloidal aqueous wax dispersions, at times mixed with emulsified siloxanes. The manufacture of such products is fairly easy and follows standard types of procedures. These type of wax- based release agents have several disadvantage: The spray mists formed during the application cause severe built up on the dies and machines, and they also block spray nozzles.
Oil-based emulsions would not cause any such problems. Unfortunately the production of so-called hydrophobic emulsions that are also stable, has, with the prevailing emulsification technologies, not been possible, so far. FOCHEM INTERNATIONAL have devoted a lot of time and energy to this problem, and eventually a new technology was developed. For the first time ever, it is possible to produce hydrophobic, nano-fine oil emulsions that appear white with slightly bluish-pink, indicating that the light is scattered off the interphases between the components of the mixture. Emulsifiers cannot be used in the formulations, as they would render the product hydrophilic with negative effect on die release.
FOCHEM INTERNATIONAL is in the fortunate position to render any type of oil, that may be suitable as a die release agent, water soluble, and most importantly “hydrophobic”. Emulsions with a solids content of up 90 % can be produced. They can be mixed with water easily forming a perfectly stable emulsion.
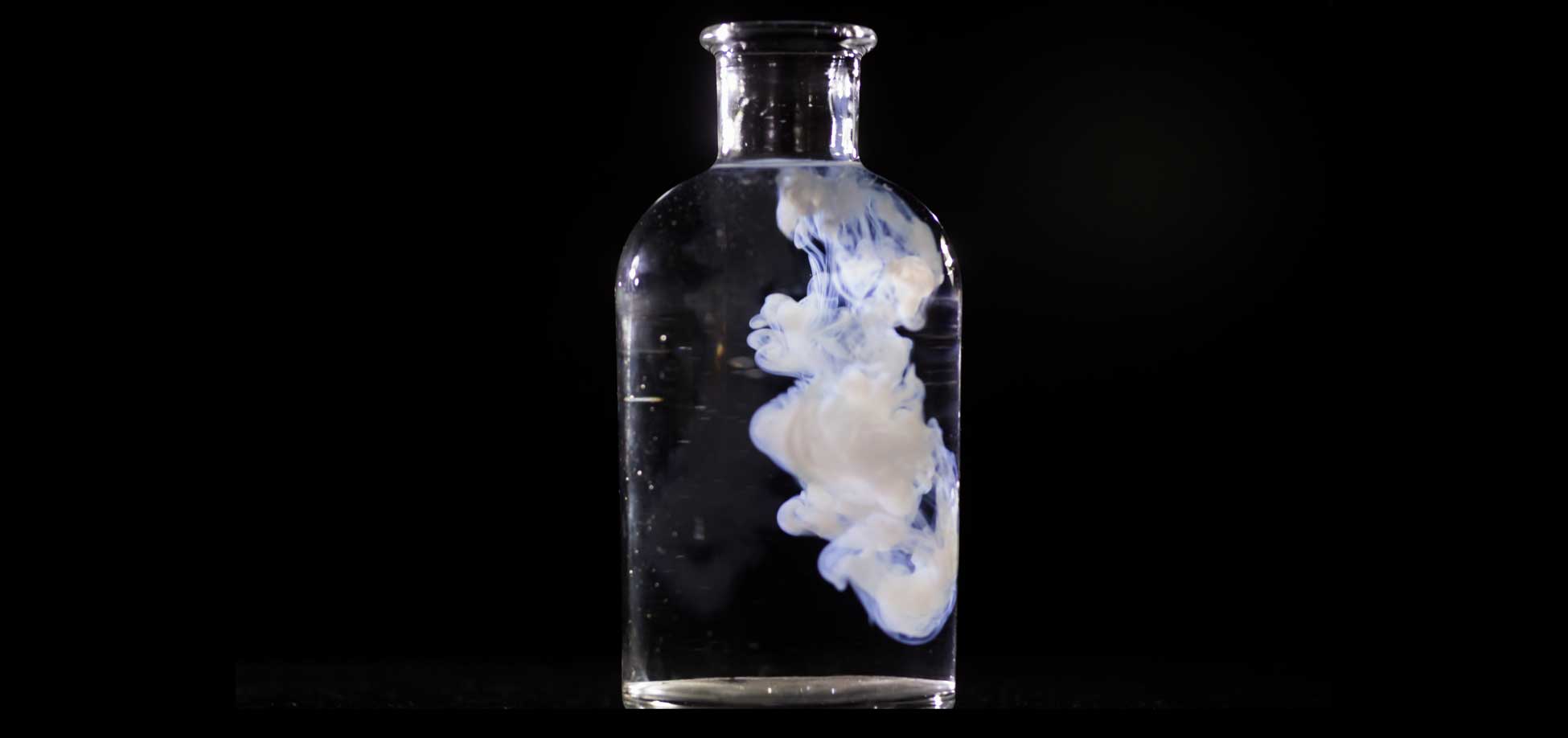
Fochem International’s Plunger Beads Technology
Originally the high pressure die-casting plunger beads had been invented in the USA some 20 years ago. This achievement was very promising as they replaced the messy graphite oils. Apart from that, the shot sleeve, especially in the case of automatic dosing, was better protected against the erosion caused by the hot aluminium smelt. For the application of the plunger beads a so-called “beads dispenser” is needed.
The initial excitement of the global die-casting industry soon ended in disillusionment. The first beads dispensers could only handle beads not smaller than with 3 mm diameters, and the melting time of such large beads was way too long. A small pipe was needed that conveyed the beads into the shot sleeve. On larger machines this pipe heated up, and the beads started melting inside the small pipe, causing blockage. The initial beads dispensers were fairly unreliable, they either dispensed too much or no beads at all. Another draw- back were the white beads offered at the time, consisting merely of wax and nothing else. They were cheap and clean, but lubrication was non-existent. Eventually the die-casters around the world switched back to oil.
FOCHEM INTERNATIONAL realised the potential of the plunger beads lubrication and embarked on new developments. They had a vision to perfect the beads by making them smaller, perfectly round, uniform in size, and with a very much higher graphite content to improve lubrication. They also devoted a great effort in the development of a reliable dispenser. During that time a so-called shuttle was invented that moves the dosing pipe out of the heat zone during the application. In the beginning the beads on the market were produced by a so-called “dripping system”, yielding only large beads which are not perfectly round.
FOCHEM developed the first beads spray technology, which, depending on the nozzles and pressures used, can yield beads sizes between 0.2 and 3 mm, as required.
Today, FOCHEM INTERNATIONAL has the most advanced beads manufacturing facility in the world, south of Johannesburg. It operates fully automatic and produces more than 200 tons of beads per month, with graphite contents up to 30 %. The beads are exported to more than 20 countries. FOCHEM’s famous “3 D Beads Dispenser” is produced by its sister company TRIBO-CHEMIE in Germany.
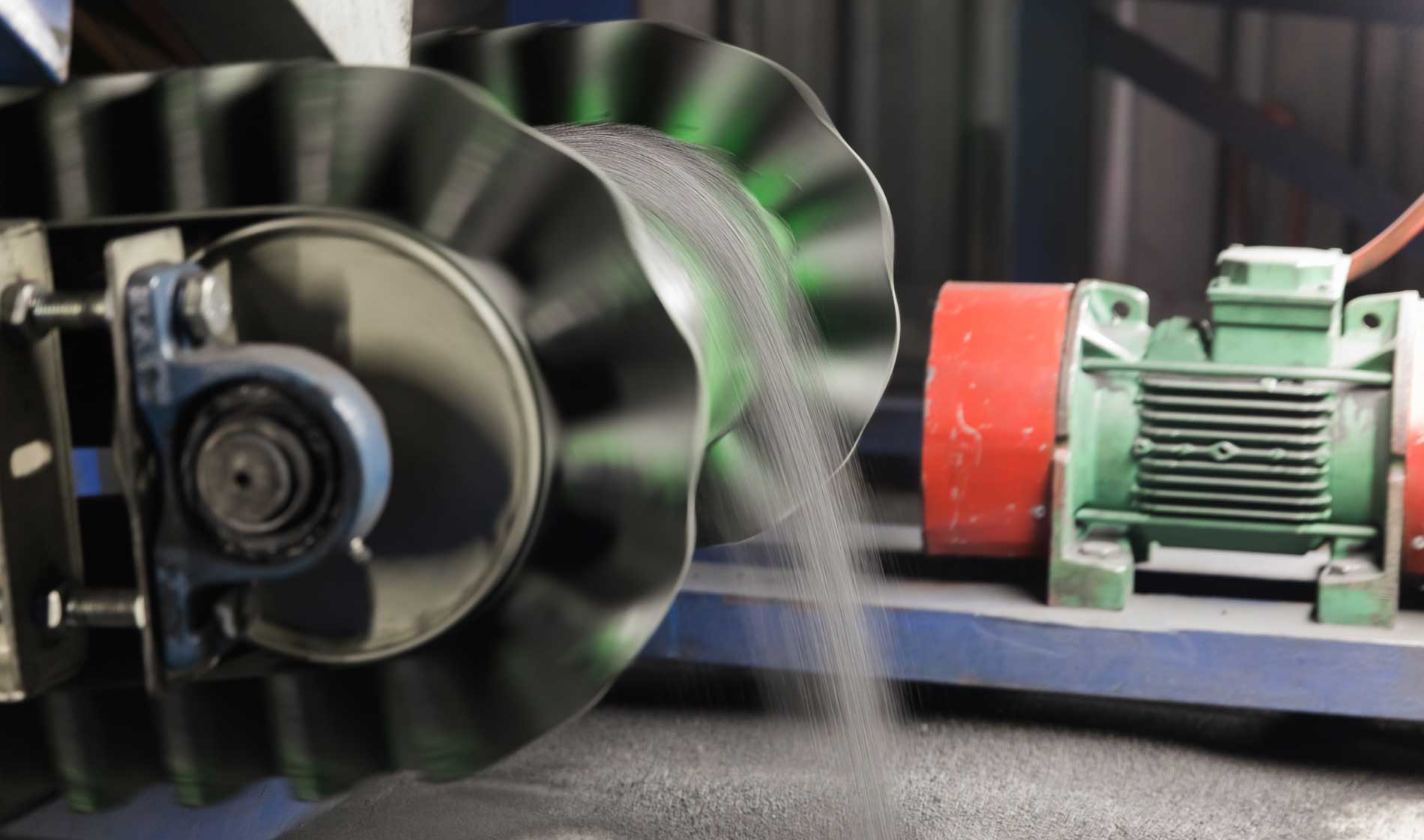